The heart of a Formula One car is its engine, while its chassis—the monocoque is its toughened shell. This structure is not only the central part of the car’s body but also a critical component for performance and driver safety.
What to know
- A monocoque is designed for F1 driver safety and is the backbone of an F1 car.
- Before a monocoque design, F1 cars were built around welded steel or aluminium frames.
- McLaren, a name synonymous with innovation in Formula One, was the first team to feature a carbon fibre monocoque.
- Producing a monocoque chassis for a Formula One car is a meticulous process, demanding absolute precision.
In this deep dive, we’ll explore the monocoque’s evolution, anatomy, materials, manufacturing techniques, and its crucial role in maintaining the high safety standards of modern F1 racing.
A history of monocoque design in Formula One
Formula One racing has been at the forefront of automotive technology since its inception, consistently pushing the boundaries of what’s possible in terms of speed, performance, and safety. The evolution of the cars reflects a relentless pursuit of innovation, one that has seen a marked transformation from the early days of using steel and aluminium structures to the revolutionary introduction of the monocoque chassis.
The switch to a monocoque construction marked a shift in the design of F1 cars, bringing with it benefits such as a jump in speed, enhanced aerodynamics, and better levels of driver protection. Before the monocoque, F1 cars were built around frames of welded steel or aluminium that provided a rudimentary shell around the driver. While these materials laid the groundwork for the early days of Formula 1 machinery, they were soon outpaced by the demands of an ever-evolving sport known for its high speeds and the constant drive for better lap times.
The monocoque chassis, with its sleek and robust shape, quickly became the foundation upon which modern F1 cars are built. The impact of its introduction was both immediate and profound, revolutionising the sport and setting a new standard for racing car design. The term “monocoque” is French for “single shell,” which describes a structural support through an external skin.; it’s a design where the car’s skin is not just a cover but an integral structural component. It allowed for more dynamic shapes, aerodynamic efficiency, and a stronger yet lighter frame.
1950s-1960s: Steel and Aluminum Chasis Structures
When Formula One was introduced in 1950, cars were built with steel or aluminium structures. The chassis design was predominantly made from sheet metal shaped and welded together, forming a bare protective shell around the driver. However, these materials had limitations in strength and safety, leading to a quest for better alternatives.
Late 1950s-1960s: The Tubular Spaceframe Era
As F1 progressed, the spaceframe chassis, made from small, lightweight tubes welded into a lattice, emerged as a superior design in the late ’50s and ’60s. It offered increased rigidity and a better strength-to-weight ratio than steel and aluminium chassis design, benefiting performance and safety. However, it still lacked the growing needs of the F1 grid, where speed and safety were being demanded by teams and drivers.
1960s Onwards: A Transition to Monocoque Construction
In the early 1960s, the monocoque chassis concept was introduced and revolutionised F1 as we know it to this day.
In 1962, the Lotus 25, the brainchild of Colin Chapman, made its debut and was at the forefront of this pioneering approach. Chapman’s innovative design allowed the car to shed unnecessary weight but significantly enhanced its aerodynamic profile. As the first Formula One car to harness the potential of monocoque technology fully, the Lotus 25 set a precedent that would dictate the future of racing car design.
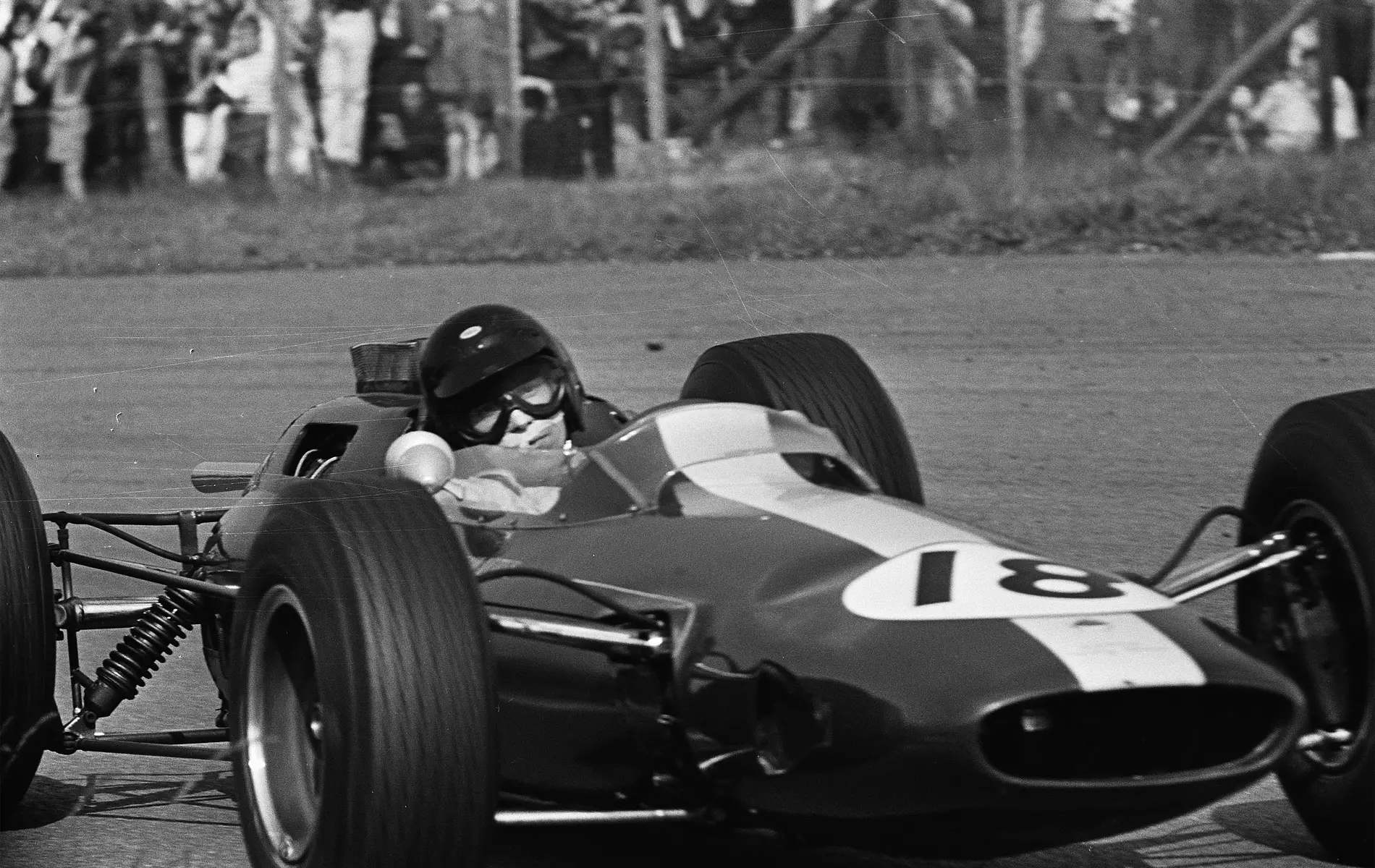
The innovation didn’t stop at the shape and weight; it extended to the materials used to construct the chassis. The 1970s saw the introduction of advanced composites like carbon fibre and Kevlar into monocoque design. These materials were game-changers, offering a combination of durability and lightness and proving to be highly effective in managing the intense stresses of high-speed racing and providing robust protection in the event of crashes.
McLaren, a historic F1 team, took things further when they unveiled their MP4/1 model in 1981, a car that was the first to feature a carbon fibre monocoque. This significant step forward in chassis design set new standards in aerodynamic efficiency, F1 driver safety, and weight management and laid down a blueprint that would become the mainstay of F1 engineering.
How is a monocoque constructed?
The monocoque of a Formula One car acts as the car’s structural backbone. It is designed to connect all other car components, from the suspension to the engine.
Structural and Safety Components
Constructed to resist the intense forces generated on the racetrack, including the substantial G-forces during cornering, acceleration, and braking, the monocoque is also built to be resilient in the unfortunate event of a collision. The safety of the driver is paramount, and as such, the monocoque’s design includes a specialised survival cell — an extremely strong section within the chassis that is engineered to remain intact and protect the driver against impacts from any direction. This cell is built from advanced composite materials that not only offer structural strength but also possess energy-absorbing qualities to minimise the force transferred to the driver during a crash.
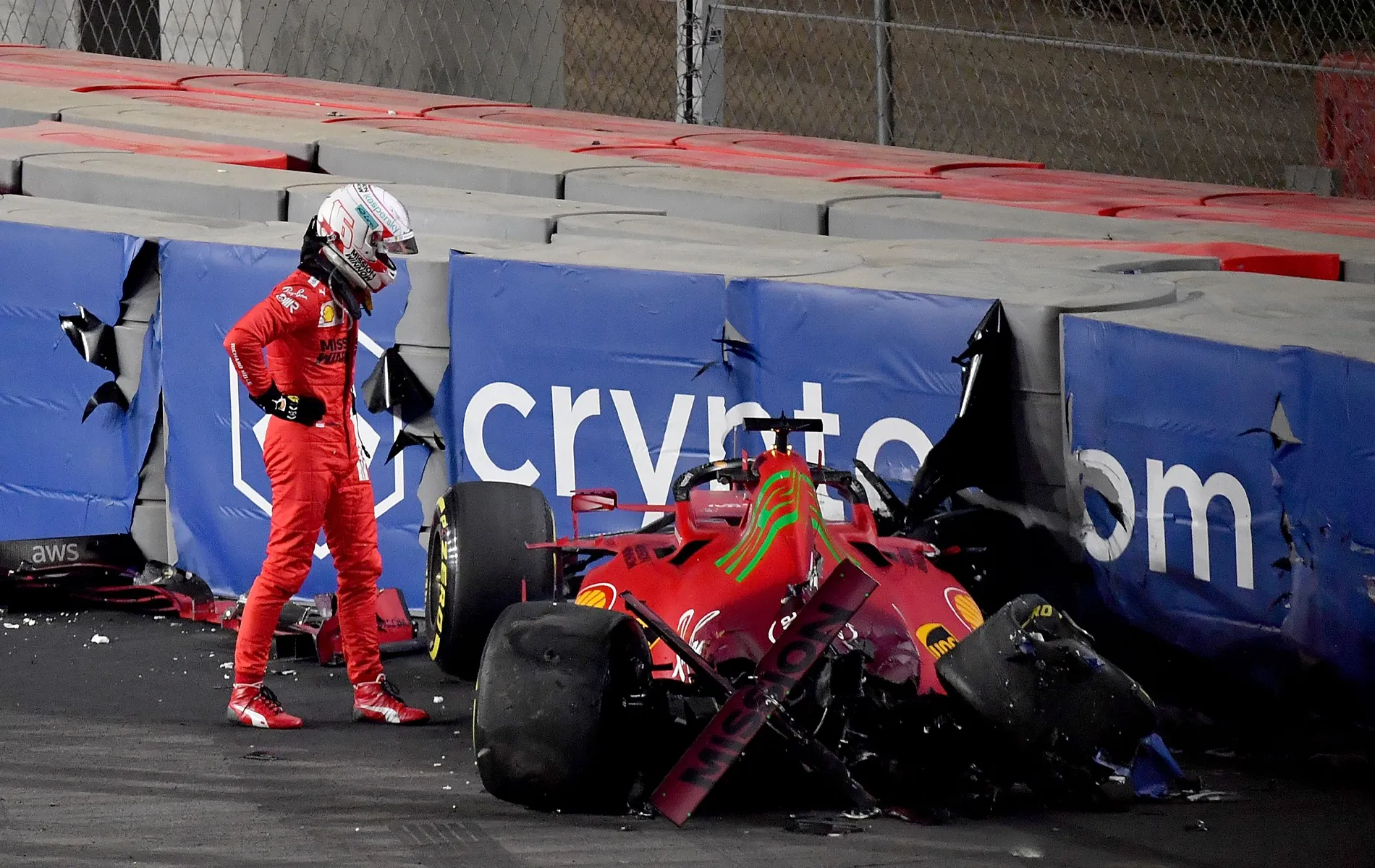
Functional and Operational Systems
Beyond its structural responsibilities, the monocoque is designed to incorporate various functional and operational systems. It houses the fuel cell, positioned to optimise weight distribution and lower the car’s centre of gravity, drivetrain, suspension, and driver, and a complex electronics network that controls the car’s functions, from engine management to data systems.
Suspension, Cooling, and Electrical
The monocoque’s role extends to being the anchor point for the car’s suspension system. It needs to provide rigid mounting points for the suspension arms and components. It also houses the cooling systems, which are essential in maintaining the engine’s performance and reliability. The monocoque will have integrated channels and ducts for air to flow through, cooling critical components. Beyond a functional role, the design must also be engineered to minimise aerodynamic drag, which is always a balancing act that requires innovative thinking and extensive testing.
The monocoque also supports nearly a mile of wiring, sensors, and control units that form the vehicle’s electrical system. This system is the car’s lifeline, controlling everything from the engine to the telemetry systems that relay information to the team in real-time. Every wire and sensor must be carefully routed and secured to avoid interference or damage while the car is being driven. The monocoque isn’t just a structural part of an F1 car but an active component that contributes to the car’s overall performance.
Manufacturing an F1 Monocoque
Built using several advanced manufacturing techniques, each selected for its unique benefits and specific challenges, the construction involved in these processes is as much an art as a science.
Hand-laid construction
Initially, composite monocoques were constructed by hand-laying carbon fibre fabrics and resin. This is a labour-intensive process and requires extreme precision and care to maintain consistency and performance. The positioning of each layer is critical, as it must be done with precision to align the fibres correctly to optimise the structural integrity and strength of the final chassis.
Autoclave curing
Autoclave Curing is a modern fabrication technique for creating a carbon fibre monocoque. This process involves placing the manually arranged composite layers into a high-tech oven known as an autoclave, where they are subjected to heat and pressure. This environment encourages the resin within the composite to cure, binding the materials into a cohesive, hardened structure that boasts strength and a superior finish.
The autoclave process does come with higher costs, mainly due to the specialised equipment. However, the investment is justified by the calibre of the end product. Monocoques constructed using autoclave curing boast exceptional strength and longevity, which make this method highly valued throughout the F1 grid.
Resin transfer moulding (RTM)
Resin Transfer Molding (RTM) is an advanced technique for manufacturing car parts. This method involves placing dry fibres into a preformed mould. Once these fibres are arranged, the mould is sealed, and a resin is injected at high pressure. This pressurised method ensures the resin permeates the fibre, resulting in a consistent resin-to-fiber ratio throughout the part.
One of RTM’s advantages is its adaptability in terms of design complexity. The process allows teams to add additional structural elements directly into the mould. This is particularly useful for building unique shapes or adding extra reinforcement to specific areas of the monocoque. While RTM may come with a higher price tag than other methods, its precision in controlling the flow and distribution of resin justifies the cost. It eliminates common issues like air gaps that can compromise the strength and integrity of a component.
Safety in F1 monocoque design
The FIA’s primary concerns in monocoque design are its structural integrity and crashworthiness, which form the cornerstone of F1 driver safety in Formula One racing. The monocoque’s role is to endure the intense stresses of high-speed racing and as a cocoon for the driver in the event of a collision.
Structural integrity and crashworthiness
As we’ve described, the monocoque is constructed using advanced materials such as carbon fibre and Kevlar, renowned for their exceptional strength-to-weight ratios. These materials are woven and layered to create a chassis that is lightweight and remarkably strong. They can absorb and dissipate energy on impact, which is crucial in a crash.
This ability to absorb energy allows the monocoque to decelerate these forces before they reach the driver. It acts like a buffer zone that reduces the severity of shocks and impacts.

Impact zones and structures
To the front and rear of the chassis, you’ll find crash structures designed to crumple upon impact. The controlled way these areas crumple allows the kinetic energy from a collision to be absorbed progressively, reducing the shock that could otherwise reach the cockpit.
Side structures reinforce the monocoque around a driver to withstand and disperse the energy from side impacts. The combination of materials and design in these side structures shield an F1 driver from the full brunt of the collision.
Survival cell
At the heart of the monocoque’s safety is the survival cell, which doubles as the driver’s cockpit. This structure is engineered to offer the ultimate protection against the worst impacts and is designed to allow for a swift exit by the driver.
The survival cell is subjected to a rigorous series of tests, all mandated and overseen by the Fédération Internationale de l’Automobile (FIA), the governing body responsible for ensuring the highest safety standards in motorsport. These evaluations are exhaustive and intended to simulate the harsh conditions of a race, ensuring that the cell can withstand extreme stresses and effectively protect the driver.
As the history of Formula One has shown us, the introduction of the survival cell has been a game-changer in driver safety and has proven lifesaving in many, many crashes. Fatalities, once a common dark side of the sport, have become increasingly rare, a testament to the safety measures in place.
Monocoque maintenance, repair and testing
Inspection and Maintenance
Post-race, the monocoque will undergo stringent inspection, maintenance and repair.
These checks are more than a cursory glance; they are comprehensive and will test for the slightest signs of wear and tear. F1 teams scrutinise the chassis with a fine-tooth comb, looking for cracks, abnormalities, or structural weaknesses. Connectors and attachments undergo similar scrutiny. This process prolongs the chassis’ performance and preserves driver safety.
Structural Repairs and Reinforcements
When there is damage to a monocoque, repairs typically involve delicately removing the compromised carbon fibre and applying new layers, cured to restore structural integrity.
Non-Destructive Testing (NDT)
Non-destructive testing (NDT) is an unsung hero in the lifecycle of an F1 monocoque. These sophisticated techniques, including X-ray, ultrasonic, and thermographic inspections, allow F1 engineers to inspect the chassis’ composite structure and diagnose issues without physically harming or testing them.
NDT is indispensable not only for ongoing maintenance but also for validating parts before they are used. By preemptively identifying defects or areas of concern, NDT helps F1 teams avoid potential failures that could compromise a race or, worse, a life.
Conclusion
The monocoque’s integration into F1 did more than enhance performance; it profoundly influenced safety, leading to advancements that have saved countless lives on the track. The once-common and often catastrophic structural failures during collisions became far less frequent. This chassis design also played a vital role in shaping the sport’s regulations, which now insist on rigorous crash tests, cutting-edge materials, and construction techniques to safeguard the well-being of drivers.
Seen in: